Corrosion-resistant Materials for Marine Spotlights in Harsh Environments
The marine environment poses significant challenges for lighting equipment because of the constant exposure to saltwater UV radiation, humidity and temperature fluctuations. Marine spotlights, which are used for applications like ship navigation, underwater exploration and offshore platforms, must withstand the harsh conditions without compromising their performance. The selection of the best corrosion-resistant material is essential to ensure longevity, reliability and safety.
Table of Contents
The Corrosive Challenge in Marine Environments
Seawater is a rich source of sodium (sodium chloride) that accelerates the deterioration of metals particularly when it is mixed with moisture and oxygen. Furthermore, exposure to sunlight and fluctuating temperatures can weaken protection coatings and accelerate fatigue. In these conditions, choosing the right marine spotlight material must be focused on strength, durability and resistance to mechanical and chemical degrading in harsh environments.
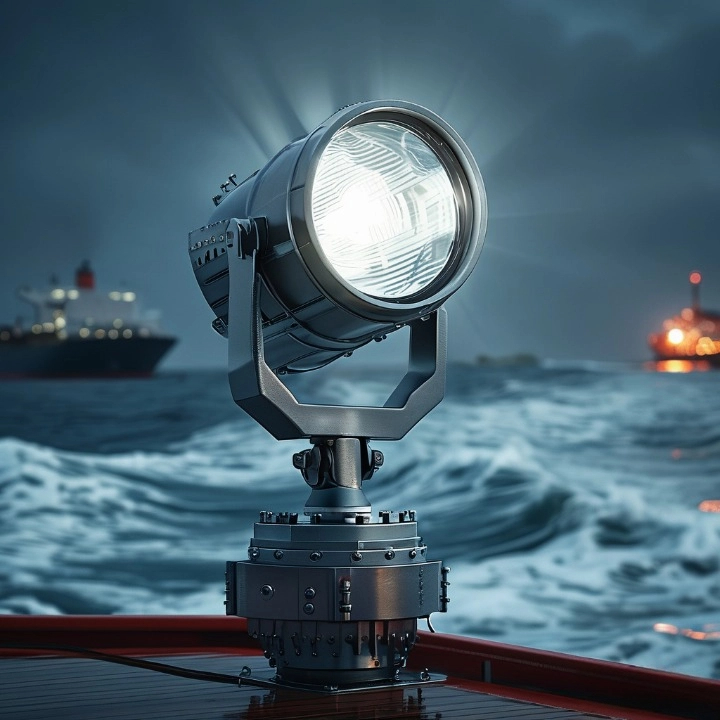
Top Corrosion-resistant Materials Used in Marine Spotlights
Corrosion poses a constant threat for marine spotlights, leading to structural damage or electrical malfunction and diminished life span. To combat this issue the marine lighting manufacturers depend on corrosion-resistant materials, both in the functional and structural components that make up the spotlight fixtures.
1. Marine-Grade Stainless Steel (316/316L)
Marine-grade stainless steel, specifically those 316 as well as 316L grades are among the most reliable substances for marine use. It is a higher percentage of molybdenum than regular stainless steel. This increases its resistance to corrosion due to crevices and pitting in environments with high levels of chloride. Low carbon levels of 316L enhances weldability and decreases the chance of corrosion in joints. Marine-grade stainless steel can be utilized as mounting brackets, spotlight housings and external fasteners. It offers outstanding durability, a beautiful polished appearance and a long-lasting service life, with little maintenance.
2. Anodized Aluminum
Anodized aluminum provides a light but durable alternative for stainless steel. Anodizing is the process by which the formation of a thick oxide layer upon the aluminium’s surfaces. This creates the appearance of a solid, non-reactive shield that is resistant to abrasion and corrosion. This is particularly useful in parts which require heat dissipation like spotlight enclosures that house the most powerful LED or Halogen lamps. Additionally, it aids in the reduction of weight, and is essential when mounting spotlights onto masts or fragile structures. Aluminum that has been anodized is usually selected for its low cost and ease of machining and superior performances in maritime environments.
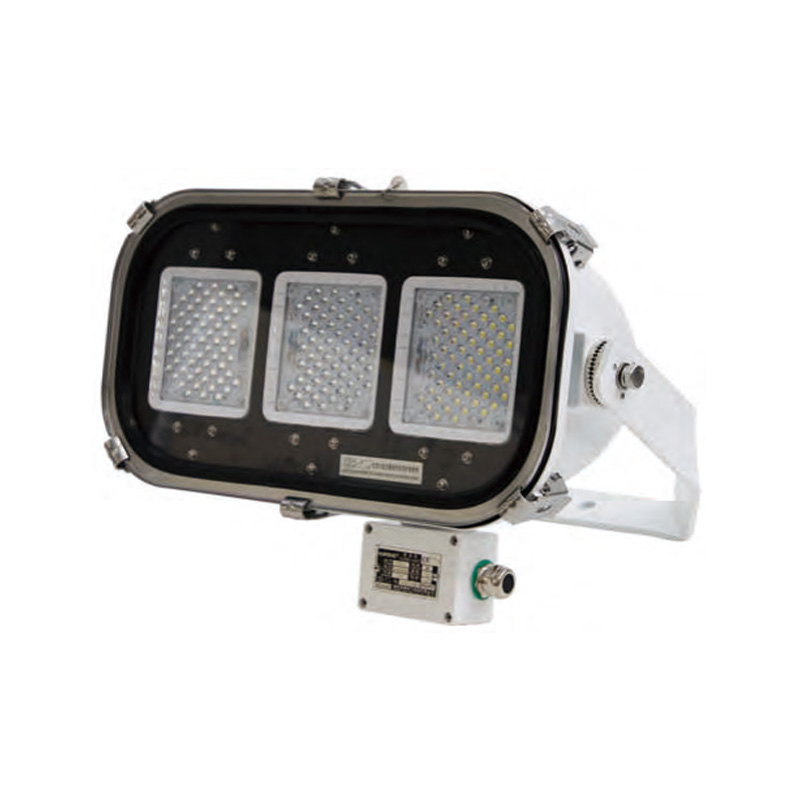
3. UV-Stabilized Polycarbonate and Engineering Plastics
Advanced plastics, such as UV-stabilized polycarbonate are being used more and more to create marine lighting designs especially as lens cover covers or housings that protect. They are non-corrosive by nature and provide excellent resistance to UV radiation and impacts. The clarity of its optical and strength makes it a great choice for covering lighting sources, while also shielding it from environmental damage. Other engineering plastics such as ABS and fiberglass-reinforced polymers are also employed, especially in applications where electrical insulation, lightweight design, and corrosion immunity are priorities.
4. Bronze and Brass Alloys
Brass and bronze are both copper-based alloys that have been extensively used in marine environments because of their inherent resistance to biofouling and corrosion. Although heavier than aluminum and not as commonly employed in large light housings, these alloys are the preferred choice for certain parts like electrical connectors, cable glands and decorative fittings. Bronze is particularly durable. can withstand corrosion even if submerged in seawater for prolonged time, which makes it a good choice for any parts that are that are exposed to splash zones or direct submersion.
5. Protective Coatings and Surface Treatments
Although they are not as a separate material coatings play an important part in improving the durability of marine spotlights. Powder coatings offer a durable beautiful, attractive and corrosion-resistant finish to metal surfaces. Electropolishing enhances the smoothness and quality of passivation in stainless steel, which reduces its susceptibility to corrosion. Paints that are marine-grade and epoxy coatings can be sprayed on steel or aluminum parts to help create a protective protection against UV and saltwater damage.
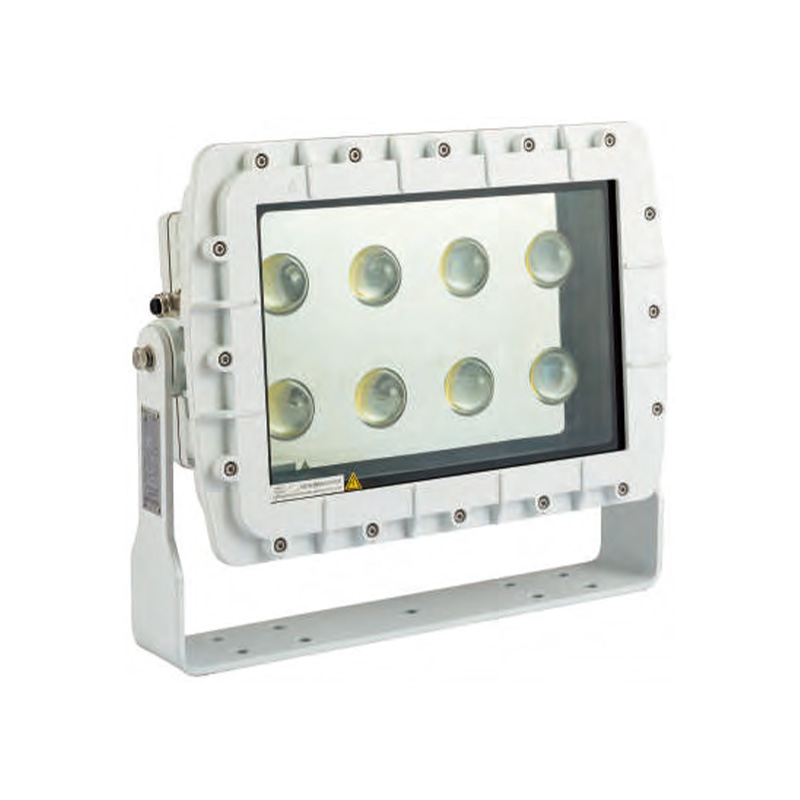
Key Factors to Consider for Choosing Corrosion-resistant Materials Used in Marine Spotlights
This chart can serve as an aid in making decisions for engineers or designers and procurement teams who are looking for the best corrosion-resistant material for marine spotlights.
Key Factor | Description | Why It Matters |
Environmental Exposure Level | Salt spray degree, exposure, UV radiation and the degree of humidity | Determines the extent of risk from corrosion and the requirements for material durability. |
Material Compatibility | The ability to prevent galvanic corrosion if different metals are employed together | This prevents electrochemical degradation and helps ensure the structural strength |
Mechanical Strength | Material’s capability to withstand impact or vibration as well as mechanical stress | The spotlight will remain operational and stable even in harsh marine conditions |
Weight Requirements | The importance of a lightweight design for deck mounting or mast | Reduces structural burden and improves the ease of installation |
Thermal Conductivity | Ability to disperse heat generated by lighting sources such as LED marine spotlight. | Maintains optimal operating temperatures and extends the lifespan of component |
UV and Chemical Resistance | Protection against degradation caused by sunlight and cleaners for marine use | Keeps appearance and integrity of material as time passes |
Ease of Fabrication and Maintenance | The ability to manufacture, shape and field maintenance | It affects the cost of production, design adaptability and the ability to repair |
Cost and Availability | The budgetary constraints and the ease of sourcing of the material | The impact of project feasibility on long-term procurement strategies |
Sustainability and Environmental Impact | Recycling and greenness of the material | It is in line with marine environmental regulations and sustainable objectives |
Expected Service Life | The life expectancy of materials is extended in extreme marine conditions. | Reduces the frequency of maintenance of the marine spotlights and repair costs over time. |
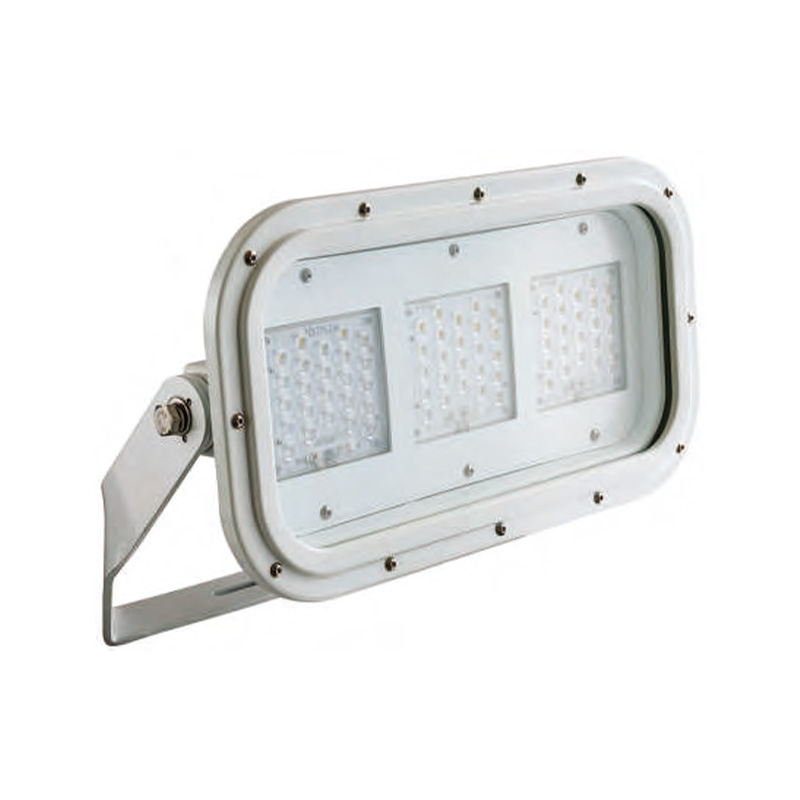
Future Trends in Corrosion-Resistant Materials for Marine Spotlights
Traditional materials that resist corrosion such as the anodized and stainless steel have been a reliable choice for the industry However, new problems with autonomous vessel construction, offshore energy along with climate change resilience, are causing an increased demand for sophisticated solutions. The future trends in corrosion-resistant marine spotlights indicate the need for advancements in material science, sustainability and intelligent functionality.
1. Advanced Composite Materials
A number of exciting trends is the application of high-performance composites, which include carbon fiber-reinforced polymers (CFRP) as well as glass fiber reinforced polymers (GFRP). These materials provide a great combination of strength, resistance to corrosion as well as weight loss. Contrary to metals, composites don’t have electrochemical corrosion issues which makes them suitable for long-term exposure to marine environments. As the manufacturing process improves and the cost of production decreases they are likely to be more widely used for housing and structural elements of marine spotlights.
2. Self-Healing Coatings
Self-healing substances are being created to repair damaged micro-elements or scratches that can affect corrosion protection. The coatings are made up of microcapsules that are filled with healing agents which are released after damage has occurred creating an insulating layer that blocks any further ingress of moisture. This is especially helpful in extending the life of brackets and housings for spotlights in situations where maintenance can be difficult or even dangerous.
3. Nano-Coatings and Surface Engineering
Nano-engineered coatings are yet another area of research in the field of marine corrosion protection. They are ultra-thin and offer superior barrier properties without the need for weight or bulk. Nano-ceramic coatings, like are able to withstand UV degradation, chemical attack and saltwater exposure much better than conventional paints. In addition, superhydrophobic nano-coatings are being investigated for their capability to resist water and other contaminants which reduces the risk of corrosion and frequency of cleaning.
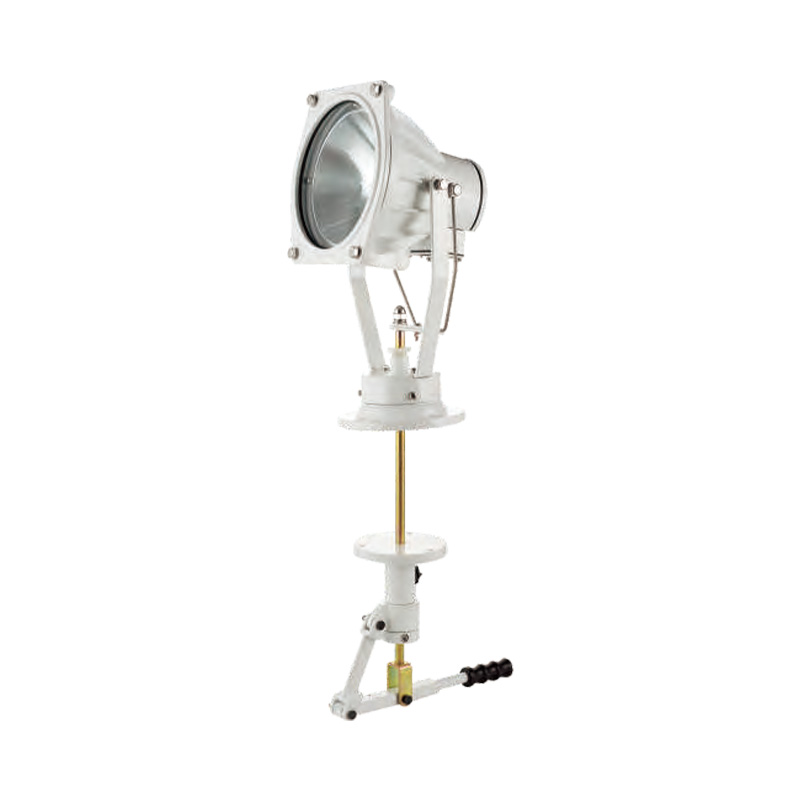
4. Bio-Inspired and Anti-Fouling Surfaces
The advancement of bio-inspired materials which mimic natural systems such as lotus leaves and shark skin are gaining attention in marine applications. These materials not only resist corrosion but also prevent biofouling which is the most frequent problem when working in marine areas. Anti-fouling materials keep the spotlight’s clarity and mechanical performance by preventing barnacle, algae and microbial growth, with no toxic coatings.
5. Environmentally Sustainable Alloys and Coatings
Sustainability is becoming a key issue across every marine industry. Future corrosion-resistant materials will not just focus on performance, but also sustainability. New alloy formulations with a reduced the amount of heavy metals, recycled composites and non-toxic, water-based coatings are being developed to meet the increasingly strict environmental regulations, particularly in marine protected zones.
6. Smart Materials and Condition Monitoring
The emergence of smart materials that are capable of the early warning indicators of corrosion is on the future. They can alter colors conductivity, as well as other properties if exposed to extreme conditions that cause corrosion. In conjunction with sensors that are IoT-enabled, these materials can provide real-time monitoring of the spotlight’s integrity that allows for maintenance with predictive accuracy and lessening the risk for sudden malfunctions.
7. Hybrid Material Systems
In the near future we’re likely to discover more hybrid structures which combine the best characteristics of several materials. For example, a composite core to reduce weight and stainless steel shells to resist impact and a nano-coating that provides corrosion protection. Multi-material systems like these can be adapted to specific usage situations, and provide superior performance in challenging marine environments.
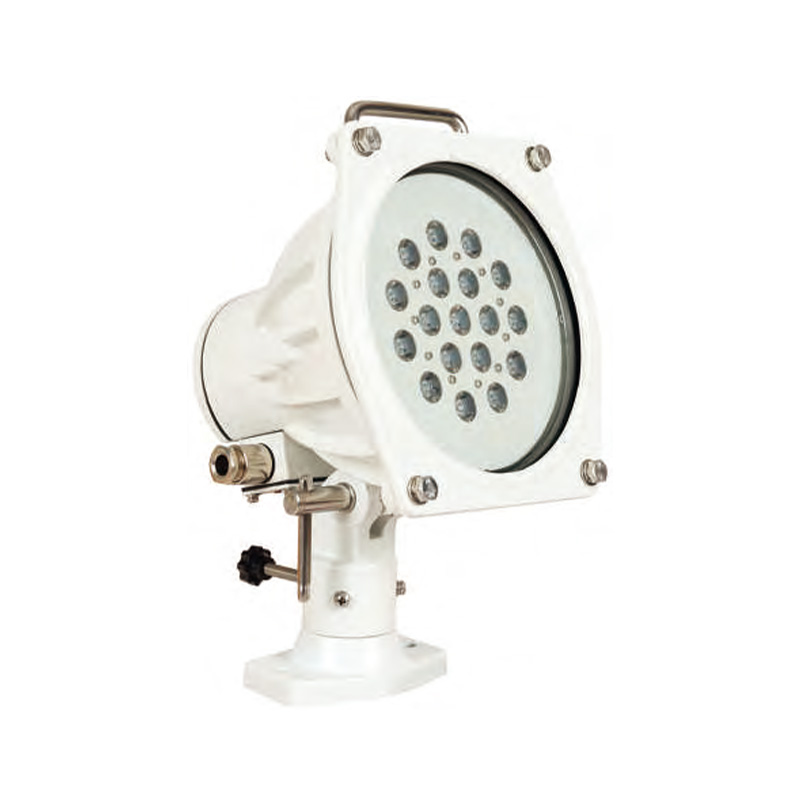
Summary
The toughness of marine environments requires an exceptional corrosion resistance from all components of marine spotlights which are crucial for operational effectiveness and safety. Through choosing durable materials such as stainless steel that is marine grade, anodized aluminum, advanced polymers and combing them with smart design and protective coatings, manufacturers can produce marine spotlights that function well throughout time, even under the toughest conditions. As technology advances, the integration of new corrosion-resistant materials that will enhance the the durability and efficiency of marine spotlights.